FORGINAL industrie's production site
The workflow of your orders and the production processes
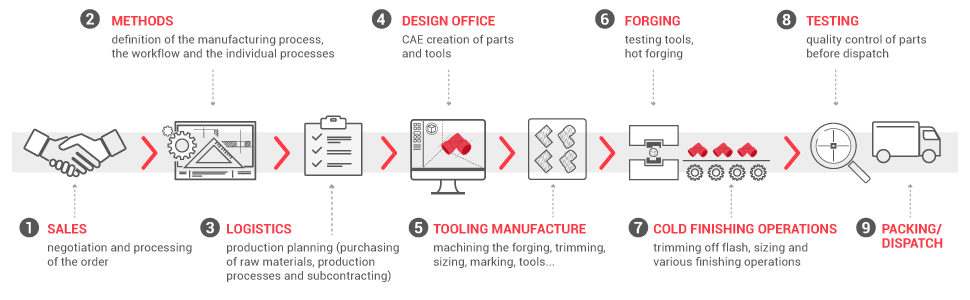
Forginal Industrie:
- Covers an area of 29,000 m².
- The buildings and land are owned by the shareholders of FORGINAL Industrie.
- The adjacent land plots allow FORGINAL Industrie to plan future expansions without any constraints.